AFO031 Oil Filtration System For The Lubricants Oil Purification System
Impurities: <1μm
Work pressure: 0.6~1Mpa
Work pressure: 0.6~1Mpa
Oil filtration systems are specialized equipment used to remove impurities and contaminants from various types of oils, including lubricating oils, hydraulic oils, transformer oils, and more. These systems are designed to maintain the cleanliness and quality of the oil, thereby enhancing the performance and lifespan of the equipment or machinery that relies on it.
Applications
Oil filtration systems find applications in various industries, including automotive, manufacturing, power generation, aerospace, and more. They are used to maintain the cleanliness of oils in engines, hydraulic systems, turbines, transformers, and other equipment.
By employing effective oil filtration systems, industries can reduce equipment downtime, improve operational efficiency, extend the lifespan of machinery, and minimize the risk of costly repairs or replacements. The specific design and features of an oil filtration system can vary depending on the intended application and the requirements of the oil being filtered.
Features
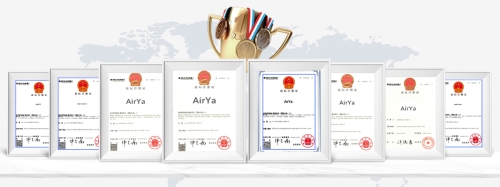
AirYa oil filtration systems use the centrifugal separation method, has the following advantages:
High Efficiency: Centrifugal separation is highly efficient in removing solid particles and water from oil. It can effectively separate and collect contaminants of various sizes, ranging from large particles to submicron-sized particles. The centrifugal force generated during the process allows for efficient separation, resulting in clean oil.
Continuous Operation: Centrifugal separators can operate continuously, allowing for uninterrupted filtration and purification of oil. They can handle a continuous flow of oil without the need for frequent stoppages, making them suitable for applications that require continuous operation and minimal downtime.
Fast Processing: Centrifugal separation is a relatively fast method for oil filtration. The separation process occurs within a short period, allowing for quick turnaround times. This is particularly advantageous in industries where time-sensitive operations are involved.
Scalability: Centrifugal separators are available in various sizes and capacities, making them suitable for a wide range of applications. They can be scaled up or down to accommodate different flow rates and volumes of oil. This scalability allows for flexibility in implementing centrifugal separation in various industries and applications.
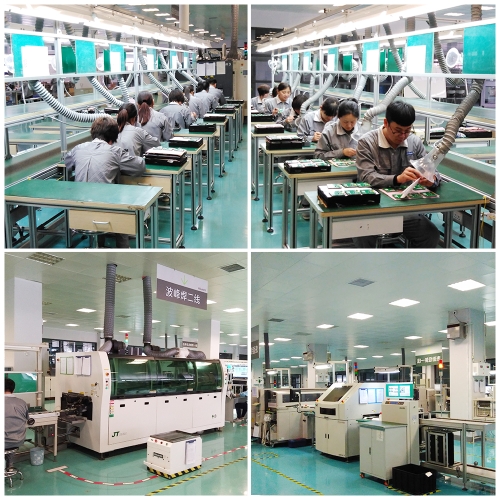
Reduced Maintenance: Centrifugal separators generally have fewer moving parts compared to other filtration systems, which leads to reduced maintenance requirements. They are designed for reliable and long-lasting operation with minimal wear and tear. This helps to minimize maintenance costs and downtime associated with system maintenance.
Versatility: Centrifugal separators can be used for different types of oils, including lubricating oils, hydraulic oils, transformer oils, and more. They are suitable for a variety of industries such as manufacturing, power generation, automotive, marine, and aviation. The versatility of centrifugal separation makes it a widely applicable method for oil filtration and purification.
Extend Equipment Life: By efficiently removing contaminants from the oil, centrifugal separation helps to protect equipment and machinery from premature wear and damage. Cleaner oil with reduced particle contamination can extend the lifespan of critical components, such as bearings, gears, and seals, resulting in improved equipment reliability and reduced maintenance costs.
Advantages
When it comes to oil filtration, the AirYa oil filtration system is a true game changer. This innovative system is designed to complete the filtration process without adding any additional oil to the oil being filtered. This is a major advantage over other filtration systems on the market that can end up diluting the oil or altering its quality in some way.
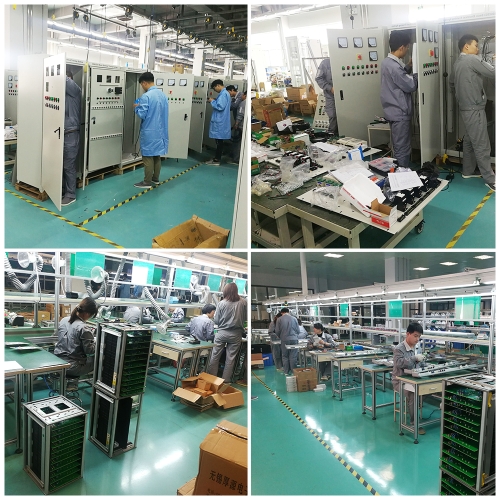
One of the key benefits of the AirYa oil filtration system is its high filtration accuracy. The system is engineered to remove even the smallest particles and impurities from the oil, ensuring that it is as clean and pure as possible. This is essential for industries and applications where the quality of the oil is critical, such as in manufacturing, food processing, and pharmaceuticals.
In addition to its high accuracy, the AirYa oil filtration system is also highly stable. The system is designed to operate consistently and reliably over long periods of time, even in demanding environments. This makes it a great choice for businesses that need a filtration system they can depend on day in and day out.
Another advantage of the AirYa oil filtration system is its versatility. The system can be used with a wide range of oils, including mineral oils, synthetic oils, and vegetable oils. This makes it a great choice for businesses that need to filter different types of oils for different applications.
Overall, the AirYa oil filtration system is a highly advanced and effective solution for oil filtration. Its ability to complete the filtration process without adding oil and without damaging the quality of the oil is a major advantage, and its high accuracy and stability make it a reliable choice for businesses of all types. If you are in need of a top-quality oil filtration system, the AirYa system is definitely worth considering.
The most important point is that there is no need for high temperature heating, no damage to the oil and the filtered oil can reach the quality of new oil.
The importance of lubricant filtration
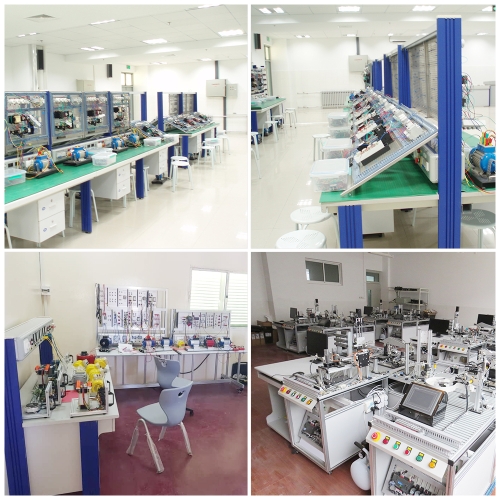
Lubricants are substances used to reduce friction and wear between moving parts in machinery and equipment. They are designed to withstand high temperatures, pressures, and other harsh operating conditions commonly found in industrial applications.
lubricants and oil filtration systems have a close relationship as they work together to maintain the performance and reliability of machinery and equipment. Oil filtration systems are designed to remove contaminants from lubricating oils, ensuring that the oil remains clean and free from harmful particles or impurities. This, in turn, helps to optimize the performance and lifespan of the lubricant, as well as the machinery it is used in. Here are some key points to understand the relationship between lubricants and oil filtration systems:
Contaminant Removal: Lubricants can become contaminated with various particles, such as dirt, metal shavings, water, and other debris, during equipment operation. These contaminants can negatively impact the lubricant's effectiveness and cause wear or damage to machine components. Oil filtration systems are responsible for removing these contaminants, ensuring that the lubricant remains clean and capable of providing proper lubrication and protection.
Extended Lubricant Life: By effectively removing contaminants, oil filtration systems help to extend the life of lubricants. Clean lubricants experience less degradation and maintain their desired properties for a longer period. This reduces the frequency of lubricant changes and associated maintenance costs, while also promoting optimal equipment performance.
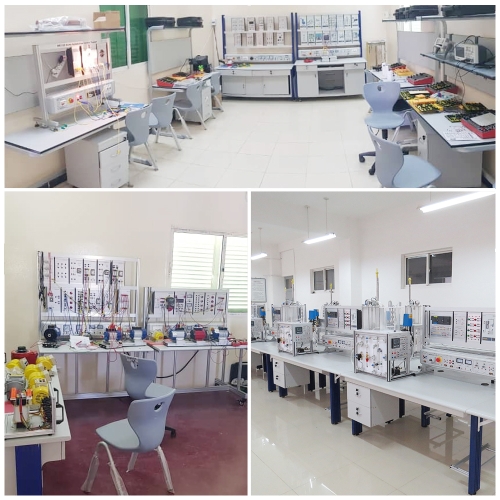
Improved Equipment Reliability: Clean lubricants play a critical role in preventing premature wear, corrosion, and component failure. When lubricants are filtered properly, they can maintain their lubricating properties and effectively protect moving parts from friction and damage. This, in turn, contributes to improved equipment reliability, reduced downtime, and enhanced overall productivity.
Enhanced System Efficiency: Contaminants in lubricating oil can increase friction and resistance within the system, leading to decreased efficiency and increased energy consumption. By removing contaminants, oil filtration systems help to maintain optimal fluid flow and reduce the energy requirements of equipment. This can result in energy savings and improved system efficiency.
Condition Monitoring: Oil filtration systems often include monitoring capabilities that allow for real-time analysis of the lubricant's condition. By continuously monitoring the oil's quality, parameters such as viscosity, contamination levels, and chemical composition can be assessed. This enables proactive maintenance, early detection of potential issues, and the implementation of corrective measures to prevent equipment failures.
Compatibility and Integration: Lubricants and oil filtration systems are designed to work together seamlessly. Lubricants can be specifically formulated to be compatible with filtration systems, ensuring effective filtration and maintaining desired lubricating properties. Manufacturers may recommend compatible filtration systems or provide guidelines on proper filtration practices to achieve optimal results.