AFM001R Collaborative 6 Axis Robot Arm With Camera And Gripper Educational Training Equipment
1. Product Overview
This equipment takes industrial robots and machine vision as the core, organically integrates mechanical, pneumatic, motion control, frequency conversion speed regulation, PLC control technology, modular structure, easy to combine, to achieve rapid detection and assembly of different materials. In order to facilitate practical training and teaching, the system has been specially designed to complete various types of robot individual training and comprehensive project training, and to complete various types of robot individual training and comprehensive project training. Six-axis robot teaching, positioning, grasping, assembly, storage and other training can be carried out, It includes six-degree-of-freedom industrial robots, intelligent visual inspection systems, PLC control systems, and a set of feeding, conveying, assembling, and warehousing mechanisms, which can implement operations such as sorting, testing, handling, assembly, and storage of workpieces. The components of the platform are all installed on the profile table. The mechanical structure, electrical control circuit and actuator are relatively independent, and are designed with industrial standard parts. Through this platform, it can be trained in various aspects such as mechanical assembly, electrical circuit design and wiring, PLC programming and debugging, intelligent visual process editing, industrial robot programming and debugging applications, and is suitable for vocational colleges and technical school automation related majors. The practical training of courses such as "Control Technology" and "Automation Technology" are suitable for automation technicians to conduct engineering training and skill competitions.
2. Technical performance
1. Input power: single phase~220V±10% 50Hz
2. Working environment: temperature -10℃~+40℃, relative humidity ≤85% (25℃), altitude <4000m
3. Device capacity: <1.5kVA
4. The size of the training platform: 1500mm×880mm×1400mm
5. Safety protection: with leakage protection, safety meets national standards
3. Practical training projects
1. Principle, use and debugging of machine vision system
2. The principle, use and debugging of the six-axis industrial robot system
3. Calibration and mutual conversion between the six-axis industrial robot coordinate system and the machine vision coordinate system
4. Installation and commissioning of integrated applications of industrial robots and machine vision systems
5. Machine vision system template setting, programming and debugging
6. Manual debugging of industrial robots through the teaching unit
7. Set and modify the coordinates of each control point through the teaching unit
8. Write and modify industrial robot programs through the teaching unit
9. Robot tracking coordinate setting
10. Software development and programming of industrial robot system
11. Intelligent visual image input editing and debugging
12. Intelligent visual results for editing and debugging
13. Intelligent visual color comparison measurement
14. Intelligent visual number comparison measurement
15. Smart visual size comparison measurement
16. Intelligent visual angle measurement
17. Integrated application of intelligent vision system and industrial robot
18. PLC program programming and debugging
19. Integrated application of intelligent vision system and industrial robot
20. Connection of inverter and main circuit of AC motor
21. Parameter setting and operation of the inverter panel
22. Frequency converter panel controls AC motor speed regulation
23. Control the motor start and stop through the external terminal of the inverter
24. Installation of pneumatic direction control loop
25. Installation of pneumatic speed control loop
26. Installation of pneumatic sequence control loop
27. Pneumatic system gas circuit connection
28. Position adjustment of auto switch
29. Pneumatic system debugging
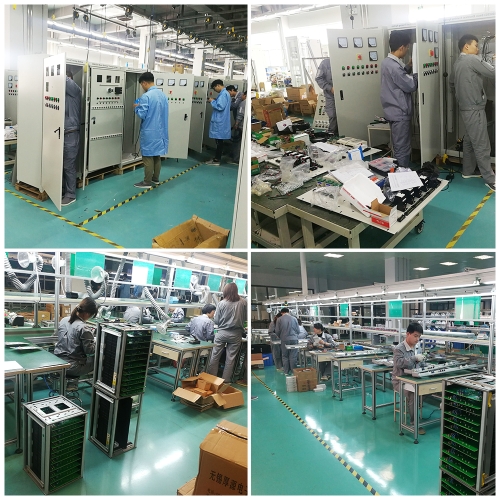